Inkjet Printing of Flat and Container Glass
The advantages and increasing reliability of digital inkjet technology are increasingly compelling – and the technology and processes now exist to accelerate its use in the glass industry – including our own curved surface compensation tool.
Inkjet and flat glass
Inkjet has already been widely adopted in flat glass printing for architectural and interior design applications. Decorative glass offers the most potential for growth as architects and designers are increasingly demanding custom glass for their projects. Another area of growth in flat glass is the need for energy efficiency, and inkjet technology contributes in this functional segment too, e.g. by changing the density of patterns printed onto the glass, architects can control how much natural light enters a specific room and how much solar heat gain typically occurs during the daylight hours in a site-specific location.
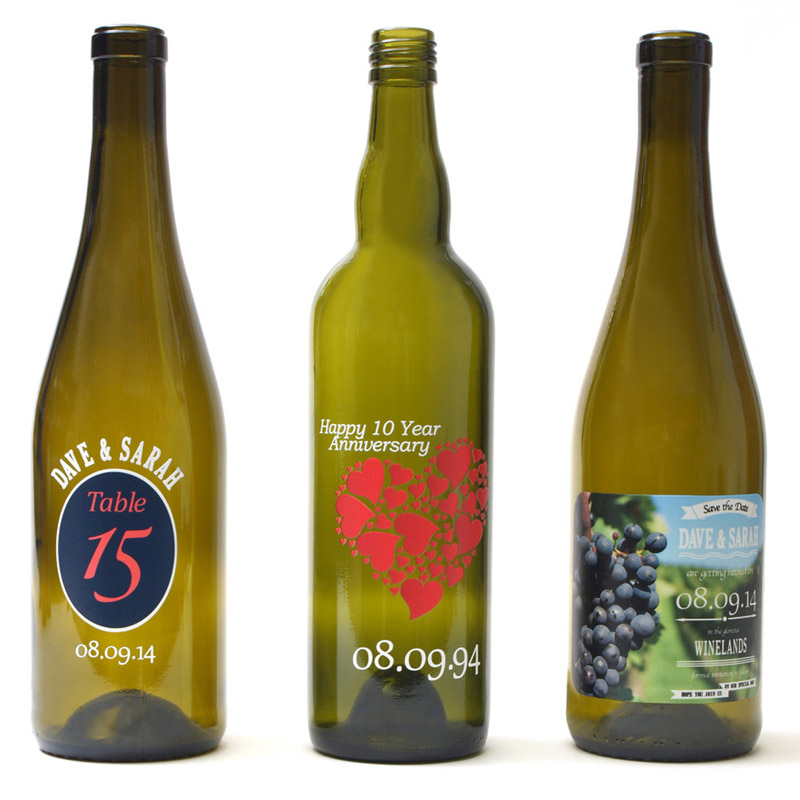
Inkjet and container glass
Inkjet printheads are designed to print onto flat surfaces, but the world of container or hollow glass is full of many different shapes and sizes. However, in recent years, inkjet technology has developed processes and techniques to print on cylinders, conical shapes and even more complex objects.
The challenge
Imagine cutting a cylinder down its length and laying it flat and you have a rectangle or square – so essentially the inkjet printers are wrapping a ‘flat’ image around the cylinder. This means also that no image compensation in software is required.
However, the physical characteristics of the printhead still create challenges. There are three key issues:
- Printhead symmetry
- Distance between nozzle rows
- The number of nozzle rows
Symmetrical orientation of the glass cylinder under the printhead is important.
Printing onto conical objects such as glass tumblers or the necks of bottles adds greater complexity and challenges for inkjet. Cut a cone down its length, lay it flat and you have what looks like a section of an old vinyl record. Image compensation is required to wrap the image around the cone – and the system also has to contend with resolution changes as the conical shape rotates under the printhead at different speeds; the image screening is more complex and the increase in drop density in the image must be compensated.
Without correction, these errors can result in unacceptable image quality, but software now exists (such as our own curved surface compensation tool) to enable printing onto conical and more complex objects. This technology is starting to be used in products for container glass printing.
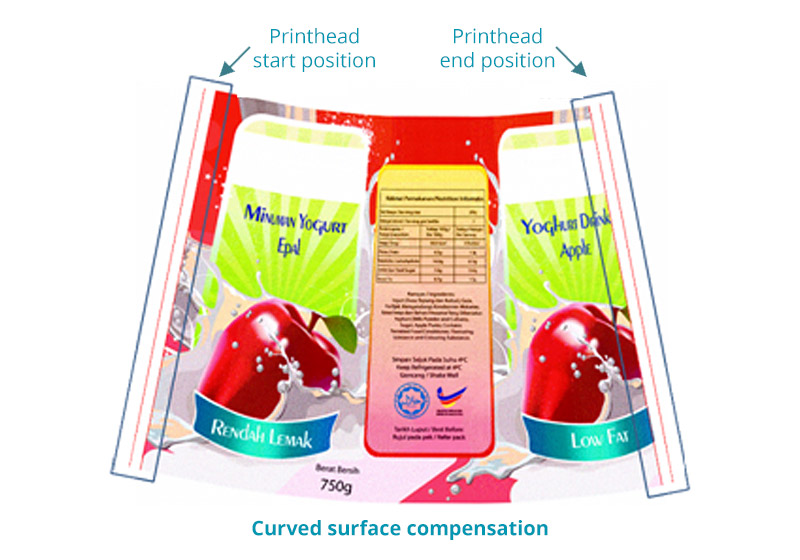
Hybrid Systems – Inkjet and Screen
With inkjet proving so versatile and inks and processes now available to print successfully onto hollow glass, does this mean that it can only be viewed as a replacement technology?
Not necessarily. There are strong arguments for hybrid systems – combining the strengths of both analogue and inkjet technologies. Screen printing offers spot colours, high density ink laydown and a homogenous, smooth surface. Inkjet offers variable data, photorealistic images, the ability to highlight structures creating novel visual and haptic effects – and much more.